The first efforts to recycle vulcanized rubber wastes originated with an ordinary grinding method carried out by Charles Goodyear, the inventor of vulcanization, more than 150 years ago. The table below gives an overview of the work done on rubber recycling, particularly in the last two decades.
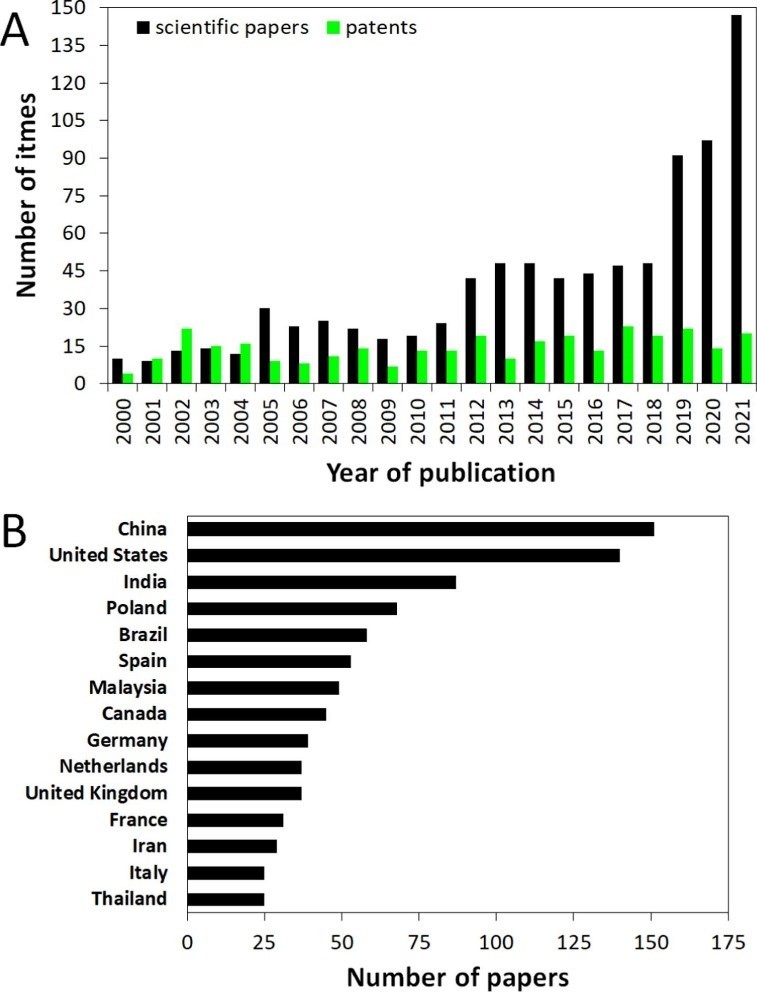
When we search Scopus again with the keyword “devulcanization”, we see the following table. We reach 484 articles published between 1928 and today (29.03.2023).
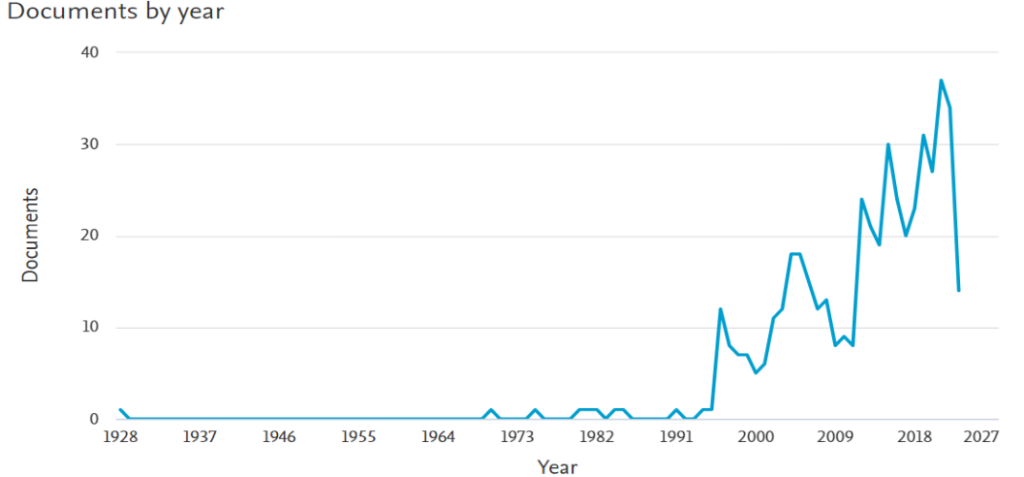
These figures show us very clearly that more research needs to be done and more technologies need to be proven in order to commercialize rubber recycling methods all over the world.
Again, when we continue to search with the keyword “devulcanization” and drill down, we see the following picture.
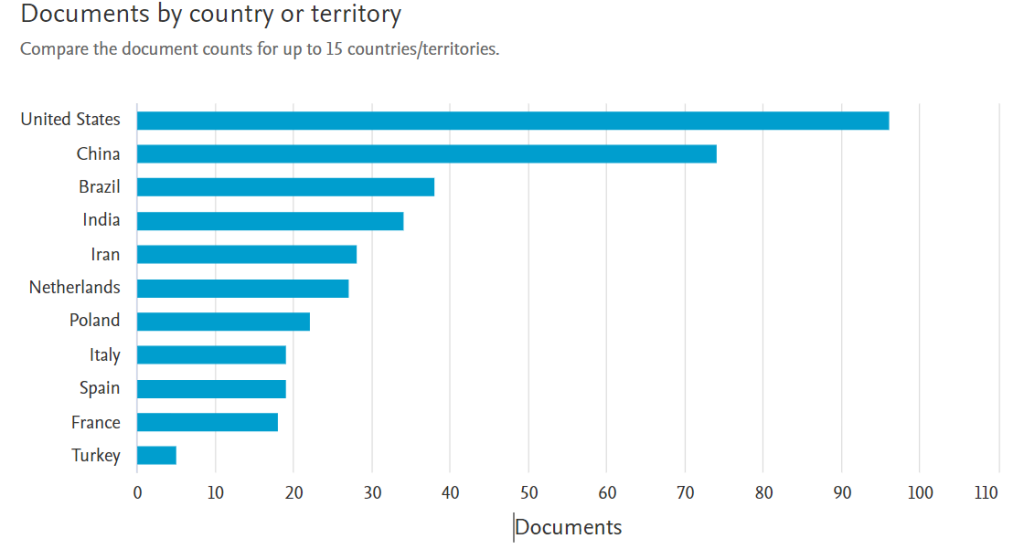
So far, published research on rubber devulcanization has generally focused on thermal, mechanical, chemical or their combination. On the other hand, literature data shows that there has not been a comprehensive review of patents covering innovative solutions that could be applied for large-scale devulcanization.
“Devulcanization vs Reclaimed Rubber”
According to ASTM D 6814, “devulcanization” is defined as the process of decomposition of chemical cross-links in cured rubber. On the other hand, ASTM D 1566 defines “reclaimed rubber” as vulcanized rubber that has been thermally, mechanically and/or chemically plasticized for use as a rubber diluent, extender or processing aid.
As can be seen, these terms are actually different, but both terms are used interchangeably in many articles and patents because they are assumed to have similar functions. In general, “devulcanization and reclaiming” represent a modification process aimed at improving the interfacial interactions between rubber and other components in mixtures, resulting in higher performance characteristics of the materials. Rubber devulcanization can be thought of as the selective breaking of cross-linked bonds to break the three-dimensional structure, while the process of “rubber reclaiming”, referred to as “reclaimed”, is a combination of main chain breaking (C-C) and indiscriminate breaking of cross-links.
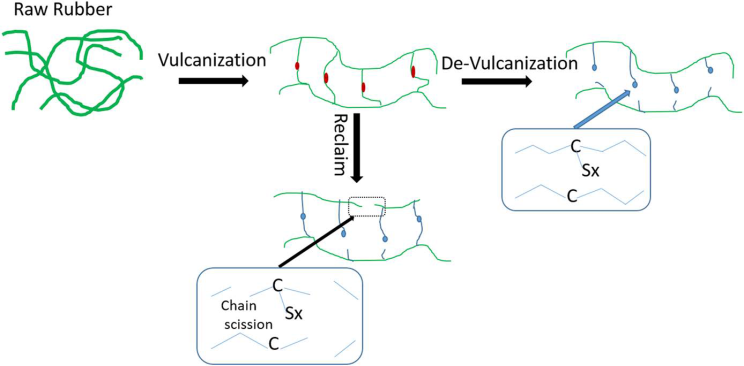
Theoretically, it is possible to break cross-links without breaking the main chain, since the energy required to break the C-C (348 kJ/mol) bond is higher than for the C-S (273 kJ/mol) and S-S (227 kJ/mol) bonds.
In practice, however, rubber products contain a greater number of C-C bonds in the main chain of the rubber than S-S crosslink bonds. Therefore, the main chain is much more likely to break. In addition, most rubber products contain various rubbers (or mixtures thereof), fillers (carbon black, silica, etc.), vulcanization chemicals and oils.
In general, vulcanization is based on breaking S-S and C-S bonds while leaving C-C bonds intact. It is the complete or partial breakdown of the monosulfide (C-S-C), disulfide (C-S-S-C) and polysulfide (C-Sn-C) bonds present in vulcanized rubber and initially formed during vulcanization. When recycling devulcanized rubber material, the degree of devulcanization affects other mechanical properties. Therefore, the physical parameters used for devulcanization should be carefully evaluated to obtain a final devulcanizate of good quality.
Due to all these disadvantages, the rubber industry is not very interested in such technologies and commercialization efforts have been insufficient. To address this issue, developments and research to selectively break sulfidic bonds without or with main chain bond breaks are still under investigation. Many existing and new devulcanization methods are being investigated by researchers, which can be grouped into 3 main categories.
Understanding vulcanization and its chemistry, the degree of devulcanization, soluble content and crosslinking density is crucial to solving this particular issue.
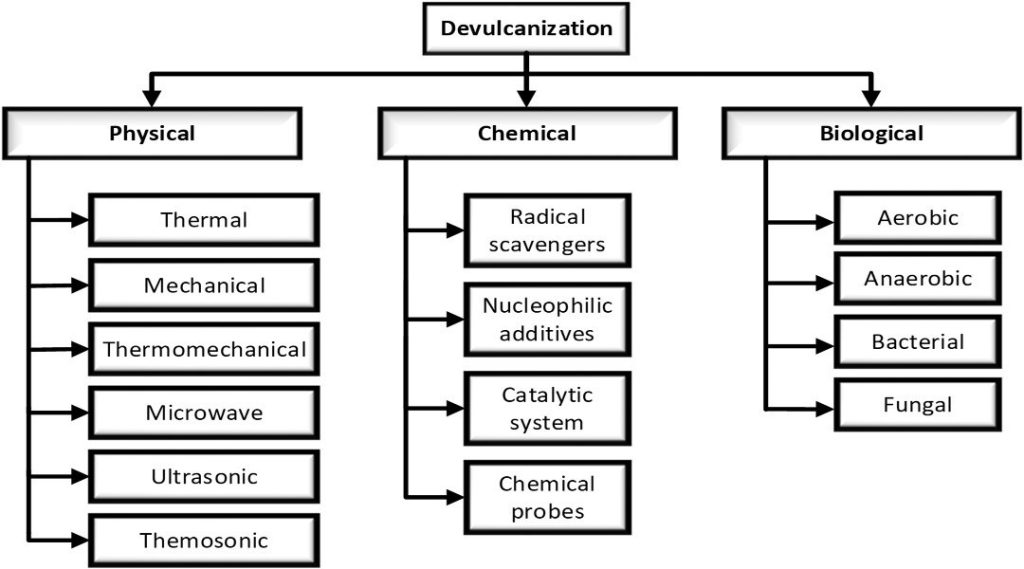
In the field of material recycling of rubber, devulcanization has gained and continues to gain even greater importance in recent years as one of the most promising approaches. Natural rubber and synthetic elastomers will continue to play an important role in industrial and domestic applications for many years to come, and at the end of their lifetime, they will be transformed into waste.
The advantages of devulcanized rubber are that the resulting rubber has a reduced carbon footprint. They can be repeatedly incorporated into the production of new products, improving circular economy, cost effectiveness, sustainability and environmental footprints.
In the case of tires, the concept of “circular economy” is rapidly beginning to make sense in developed countries and research continues, but in other countries of the world, this awareness has not yet been established. For general rubber products, circular economy is almost non-existent. Better sorting, collection and initiatives for non-tire and general rubber products continue to be sorely needed for a healthy rubber waste management and the establishment of a circular economy.
#ICarbon, which continues its R&D studies with the aim of developing devulcanization technologies and is the only company researching in this field in our country, continues to develop devulcanization methods that will gain great importance in the future.
It is not over yet, of course it is not possible for it to end 🙂 … Our series will continue with our articles in which we will interpret devulcanization technically and scientifically…
Yours sincerely
Erdem Mutlu – ICARBON Founder