Carbon black is a dominant filler used in industrial rubber products, vehicle tires and many plastic parts. Sustainability issues and the desire to produce energy efficient products are increasingly driving OEMs and other carbon black users to find alternatives and develop more environmentally friendly material options. Growing awareness of environmental issues, particularly related to vehicles and tires, is creating more demand for sustainable carbon black options.
According to a recent report by Smithers, technologies that support sustainable carbon black production are becoming increasingly in demand and will contribute 2 million tons to the global carbon black supply by 2041. This is equivalent to approximately 20 conventional furnace carbon black production lines.
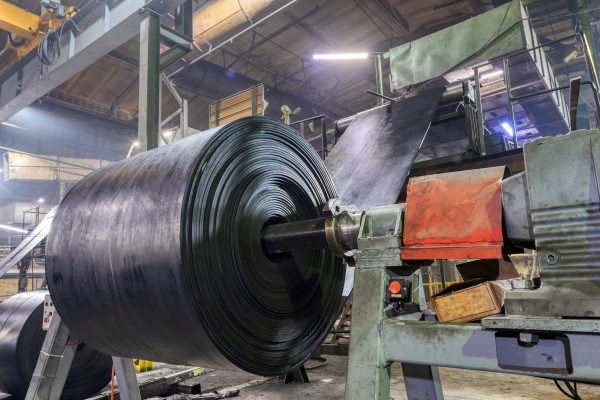
According to Smithers, four leading technologies are expected to develop over the next two decades to meet the growing demand for more environmentally friendly alternative materials to fossil-based carbon black.
Methane Pyrolysis is an alternative to furnace black production and a pilot line is already in operation. This is less energy intensive than furnace black production. While the pilot line is configured to use natural gas as an input, there is potential to develop the technology to also run on bio-gas or bio-methane. For end users, the key requirement beyond scale-up is improvements to allow methane pyrolysis to produce harder, more durable grades of carbon black.
Reclaimed Carbon Black (rCB); Recycling tires in general is becoming an increasingly popular option. rCB is a high potential future sustainability option for 65% of tire OEMs. Its production is up to 85% less carbon neutral than furnace black and requires no direct petroleum inputs. rCB will never be completely carbon neutral as its recovery and preparation requires heat treatment. More work needs to be done to establish specifications and quality control and the current generation of rCB technology needs to be improved to produce harder blacks.
Renewable Carbon Black is produced by using biogenic materials such as wood instead of petroleum inputs. It uses existing furnaces with minimal modification and can produce conventionally harder grades of black. The biggest flaw of this approach is cost. Prices five to ten times that of conventional carbon blacks make this technology an unrealistic option for the mass market at the moment.
The final option is Cyclic Carbon Black, a solution that again takes advantage of the availability of end-of-life materials. Unlike rCB processing, this requires the intermediate step of first converting used tires or polymers into pyrolysis oils.
Cyclic carbon black still produces carbon emissions, but the energy use is much lower than conventional carbon black processes. It can produce high-performance reinforcement grades, but the cost is at least twice that of conventional furnace operations and this is a major obstacle.
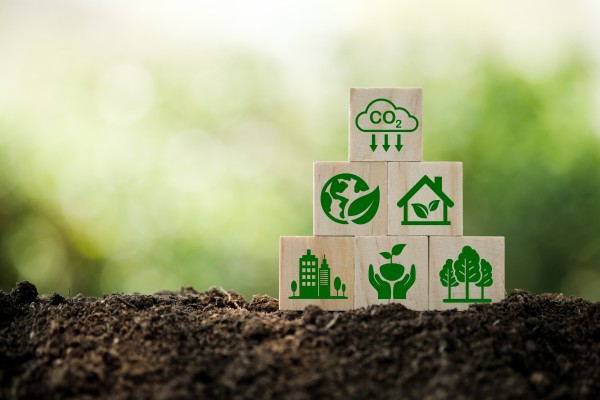
Last but not least, the industry needs to raise awareness and will for the rapid development of technologies that are still in their infancy. You can be sure that ICarbon, which continues its R&D efforts to contribute to all four solutions, will continue to develop methods that will meet the future demands to reduce costs and improve the quality of carbon blacks produced for a sustainable world.
We will continue to write about all these technologies…
Erdem Mutlu – ICARBON Founder